Сварка и наплавка при ремонте деталей и сборочных единиц
При текущем ремонте оружия в войсковых ремонтных органах широко применяется электродуговая и газовая сварка.
Газовая сварка применяется обычно тогда, когда не может быть применена электродуговая сварка. Так, газовая сварка позволяет производить соединение тонкостенных и листовых стальных деталей, а также сваривать и наплавлять детали из чугуна, цветных металлов и их сплавов.
Кроме того, газосварочный шов мягче и легче обрабатывается, чем шов, полученный электросваркой. С помощью газовой сварки можно наплавить мелкие детали, получая точное соединение более высокого качества, чем при электродуговой сварке.
Однако газовой сварке присущи и недостатки. Она менее экономична и менее производительна, чем электродуговая сварка. Газовая сварка имеет сравнительно сложное оборудование, взрывоопасна при эксплуатации; кроме того, возможно замерзание воды в генераторе при. низких температурах окружающего воздуха. Характерными сварочными работами являются заварка трещин, соединение поломанных деталей, заделка пулевых или осколочных пробоин и наплавка металла на изношенные поверхности деталей.
Сварка и наплавка деталей производится в помещении с температурой не ниже 5° С.
При проведении сварки при температуре ниже 5° С место сварки предварительно прогревается до 30—50° С и защищается от ветра во избежание быстрого остывания детали; а при сварке на открытой площадке, кроме того, деталь защищается от атмосферных осадков (дождь, снег).
Способ наплавки или заварки деталей (электродуговая или газовая сварка), а также марка электрода или марка сварочной проволоки должны соответствовать указаниям руководства по ремонту образца оружия.
Технологический процесс ремонта разрушенных стальных деталей электросваркой слагается из подготовки детали, выбора электрода (если он не указан в ремонтной документации), подогрева, сварки и последующей термической, слесарной или станочной обработки.
Подготовка детали к сварке заключается в очистке поверхности и разделке кромок под сварку.
Поверхности деталей, подлежащие сварке или наплавке, предварительно очищают до металлического блеска от ржавчины, грязи, смазки и краски. Очистке подвергают также поверхности, прилегающие к восстанавливаемому участку на расстоянии 20—40 мм. Очистку производят шлифовальной шкуркой, кардолентой, напильником или шабером. Затем очищенный участок обезжиривают уайтспиритом.
Подготовка кромок детали к сварке производится обычно зубилом, крейцмейселем или напильником.
Качество и механические свойства шва, полученного в результате сварки, в значительной мере зависят от типа и марки электрода, поэтому в ремонтной документации для каждого случая сварки указываются типы электродов по ГОСТ 9467—60 и ГОСТ 10051—62, каждому из которых соответствует несколько различных марок.
В отдельных случаях при отсутствии данных о типе или марке электрода при сварке электрод подбирается по соответствующим таблицам, помещенным в Общем руководстве по ремонту, ч. I, в зависимости от марки стали, из которой изготовлены свариваемые детали, а при наплавке — в зависимости от требуемой твердости наплавленного слоя металла ino таблицам указанного руководства.
Для улучшения качества сварки рекомендуется сушка электродов при температуре 120—150° С в течение 2 ч.
Детали крупные, сложной конфигурации и переменного сечения, а также изготовленные из высокоуглеродистых и легированных сталей во избежание коробления и появления значительных местных остаточных напряжений подвергаются предварительному нагреванию в зоне сварки. Кроме того, подогрев деталей перед сваркой производится для того, чтобы предотвратить появление трещин, образующихся вследствие усадки металла шва. Образование трещин наблюдается обычно у деталей из стали с содержанием углерода свыше 0,4% и из легированных сталей с повышенным содержанием хрома, никеля, кремния, марганца и других элементов, например, стали марок 30ХГС, 30ХМА, 33ХГC, 35ХМА и т. п.
Детали нагревают паяльлой лампой, в кузнечном горне, в печах или другим способом до температуры 250—300° С и на рабочем месте при сварке во избежание быстрого охлаждения укрывают различными теплоизоляционными материалами (асбестом, горячим песком и т. п.).
Режим сварки, диаметр электрода и силу тока определяют в зависимости от толщины свариваемого материала, вида сварного соединения и марки электрода (если последний не указан в руководстве).
Ориентировочно режим сварки может быть назначен в соответствии с рекомендациями табл. 14.
Таблица 14
Параметры |
Толщина свариваемой детали, мм |
||||
До 3 |
3 - 4 |
5 - 6 |
7 - 8 |
свыше 8 |
|
Диаметр электрода мм |
2 |
3 |
4 |
5 |
6 |
Ток, А |
80 - 120 |
160 - 180 |
200 - 240 |
240 - 300 |
230 - 340 |
Приближенно рассчитывать величину тока можно по формуле I = 50 d где d — диаметр электрода в миллиметрах.
Сварку и наплавку следует производить по возможности при постоянной длине дуги: сварка короткой дугой приводит к перегреву металла, сварка длинней дугой — к непровару и разбрызгиванию металла. Наклон электрода должен быть постоянным и равным 15—20° от вертикали в сторону его движения.
В необходимых случаях после сварки производится термическая обработка детали для уменьшения остаточных напряжений.
Выбор марки присадочной проволоки для газовой сварки производится по ГОСТ 2246—70.
Одним из наиболее распространенных и эффективных способов ремонта стрелкового оружия является наплавка металла на изношенные поверхности деталей с последующей слесарной или станочной обработкой. Она позволяет восстановить нормальные размеры деталей, обеспечить правильное взаимодействие частей, устранить качку и ненадежность соединения.
Подготовка детали к наплавке заключается в очистке наплавляемой поверхности и ее опиловке на 1—3 мм. Снятие небольшого слоя металла детали необходимо потому, что переходной слой между основным и наплавленным металлом при наплавке значительно перегревается, приобретает крупнозернистую структуру и сильно засоряется шлаком и окислами.
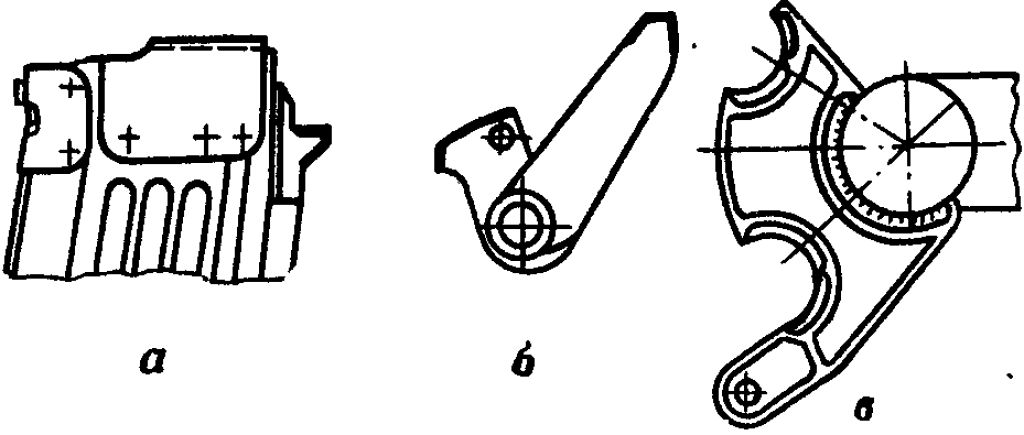
Рис. 119. Примеры наплавки поверхностей деталей стрелкового оружия:
а — упора магазина АК; б — автоспуска АК; в — стенок полукруглых вырезов в кулаках осей хода ЗПУ-4
Толщина этого слоя составляет 0,5—1 мм. Для того чтобы металл поверхности, обработанный после наплавки, имел однородную структуру, нужно до наплавки снять с поверхности слой толщиной 1—3 мм.
Наплавка поверхности заключается в последовательном наложении наплавляемых валиков с припуском на дальнейшую обработку.
Наплавленный металл шва должен выступать над основным металлом не более чем на 1—2 мм.
При большей высоте наплавленного металла в месте перехода от шва к основному металлу возникают повышенные напряжения, понижающие механические свойства наплавленного металла и основного металла.
Обработка деталей после наплавки заключается в опиловке наплавленной рабочей поверхности и наплывов металла напильником или в обработке другим способом до размеров, указанных в руководстве по ремонту образца оружия, с последующей пригонкой деталей по месту, если это требуется.
Места наплавки и обработки деталей на рисунках и чертежах в ремонтной документации показываются жирными линиями. При этом даются только те размеры, которые необходимы для выполнения операций механической или слесарной обработки детали после наплавки.
На рис. 119 показаны некоторые примеры ремонта деталей стрелкового оружия путем наплавки.